"Galvanizing is galvanizing. Hot-Dip Galvanizing is the same as any other type of galvanizing."
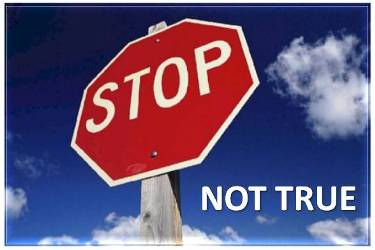
After fabrication, hot dip galvanizing is specified by ASTM A123 and generally refers to fabricated assemblies typically used in petrochemical facilities, power transmission applications and offshore equipment assemblies, although, other materials such as unfabricated (stock) members are also included in the specification. ASTM A123 clearly identifies these materials in section 1.
This specification covers unfabricated and fabricated products such as:
- Assembled steel products
- Structural steel fabrications
- Large tubes already bent or welded before galvanizing
- Wire work fabricated from uncoated steel wire
- Steel forgings and iron castings incorporated into pieces fabricated before galvanizing or which are too large to be centrifuged
*It does not apply to wire, pipe, tube or steel sheet which is galvanized on specialized or continuous lines, or to steel less than 22 gage (0.0299 in.) [0.76 mm] thick.
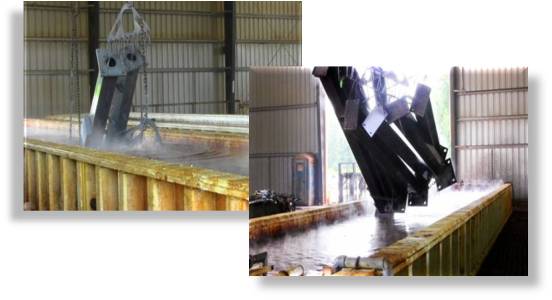
Different types of zinc coatings:
- Hot Dip Galvanizing – Hot dip galvanizing is achieved by immersing cleaned steel products in molten zinc at 830 0F – 850 0F. When the base metal comes into contact with molten zinc at this temperature, the zinc and iron combine in a “diffusion reaction” forming new metallurgically bonded zinc/iron alloy layers. The new layers (galvanizing) serve as a super-bonded abrasion resistant barrier, as well as providing cathodic protection. A metamorphosis takes place when the steel and molten zinc react together, forming a series of zinc-iron alloy layers which are: Eta (100% zinc), Zeta (94% Zinc, 6% Iron), Delta (90% Zinc, 10% Iron), and Gama (75% Zinc, 25% Iron).
- Zinc Metallizing – Metallizing or zinc spraying is accomplished by feeding the zinc in either wire or powder form to a spray gun where it is melted and sprayed onto the steel surface. Metallizing allows coating of fabricated items, which cannot be galvanized due to their size. Metallizing is an ASTM approved method of repair of damaged or uncoated areas on galvanized steel. Before metalizing, abrasive cleaning of the steel to white metal is required. Metallizing provides cathodic protection but does not develop the zinc/iron alloying (metallurgical bonding) found with hot dip galvanized products.
- Zinc Rich Paint – Zinc rich paint consists of zinc dust suspended in organic or inorganic binders. Zinc rich coatings are barrier coatings, which can also provide some limited cathodic protection. The binder must be conductive or the zinc particles must be in contact with the steel substrate to provide cathodic protection. The coating does not develop zinc/iron alloys. Suitable zinc rich paints are approved by ASTM as repair coatings for damaged galvanized coatings.
- Continuous Galvanizing – Continuous galvanizing is a hot dip process, although usually limited to steel mill operations. The process consists of coating sheet steel, strip or wire on machines over 500 feet long, running material at speeds of over 300 feet per minute. The mil thickness is minimal compared to that of hot dip galvanized after fabrication, with minimal zinc/iron alloy layers; however, barrier and cathodic protection is provided.
- Zinc Electroplating – Electroplating generally refers to a very thin layer of zinc coating applied to steel sheet and strip by electro-deposition in a steel mill facility. There are no zinc/iron alloy layers, however, barrier and cathodic protection is provided.
The American Galvanizers’ Association (AGA) maintains a website with access to a wealth of information about the industry. Newsletters, press reports, specification and fabrication guidance, technical papers, and more is available.
**The most important thing a designer and/or fabricator can do to maximize the probability of achieving a quality galvanized product, is to consult the galvanizer during the design process.