In manufacturing, quality control is a top priority, especially when it comes to structural integrity. One common practice among manufacturers for maintaining high quality is the thorough inspection of complete joint penetration (CJP) welds. These welds, often found on thick plate materials such as base plates or flange plates, play a crucial role in the strength and durability of large structures like transmission poles and frameworks. A common quality inspection used on these structures is Ultrasonic Testing (UT). In this blog, we’ll dive into the types, benefits, and challenges of UT Testing.
What is UT Testing?
Ultrasonic testing (UT) is a non-destructive testing (NDT) technique that allows manufacturers to assess the internal quality of welds without compromising the material. This method uses high-frequency sound waves to identify flaws within welds, measure thickness, and evaluate material properties. UT testing operates by transmitting ultrasonic waves—ranging from 0.5 to 20 MHz—through a material.
A quality control technician uses a transducer to emit these ultrasonic waves into a weld. As the waves move through the material, they reflect off any inconsistencies or flaws and return to the transducer. The transducer then converts these reflected waves into electrical signals, which are displayed on a screen for interpretation. By examining these signals, technicians can pinpoint internal defects that may otherwise be invisible to the naked eye.
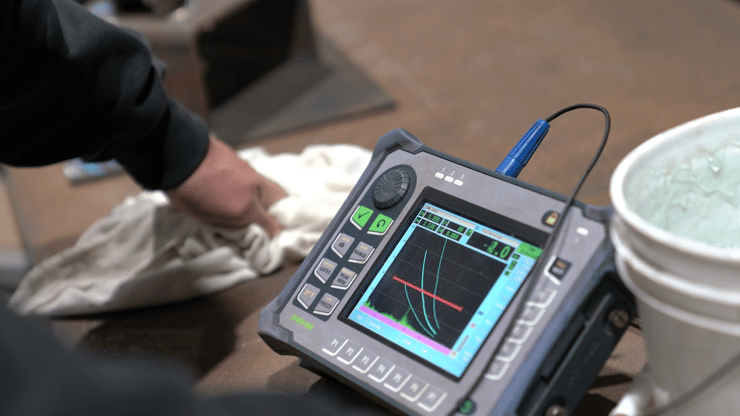
Types of Ultrasonic Testing Methods
There are several types of ultrasonic testing methods commonly used in quality control. These include:
- Pulse-Echo Testing
This is the most common type which involves sending pulses into the material and measuring echoes that return. When echoes reflect back to the transducer, it indicates a flaw, such as a crack or void.
- Through-Transmission Testing
This technique uses two transducers positioned on opposite sides of the material. If there are flaws, they interrupt the signal transmission, allowing technicians to spot defects quickly. Through-transmission is often used when evaluating thickness and identifying internal cracks.
- Phased Array Ultrasonic Testing (PAUT)
PAUT is an advanced technique that uses multiple ultrasonic probes in a phased array to scan a weld. By steering and focusing sound waves at varying angles, PAUT provides detailed images and data that allow technicians to assess complex structures accurately.
- Time-of-Flight Diffraction (TOFD)
TOFD utilizes two transducers, one to transmit and one to receive. It is ideal for identifying and sizing defects with high accuracy and is commonly used in the inspection of high-stakes materials, such as those in aerospace or nuclear industries
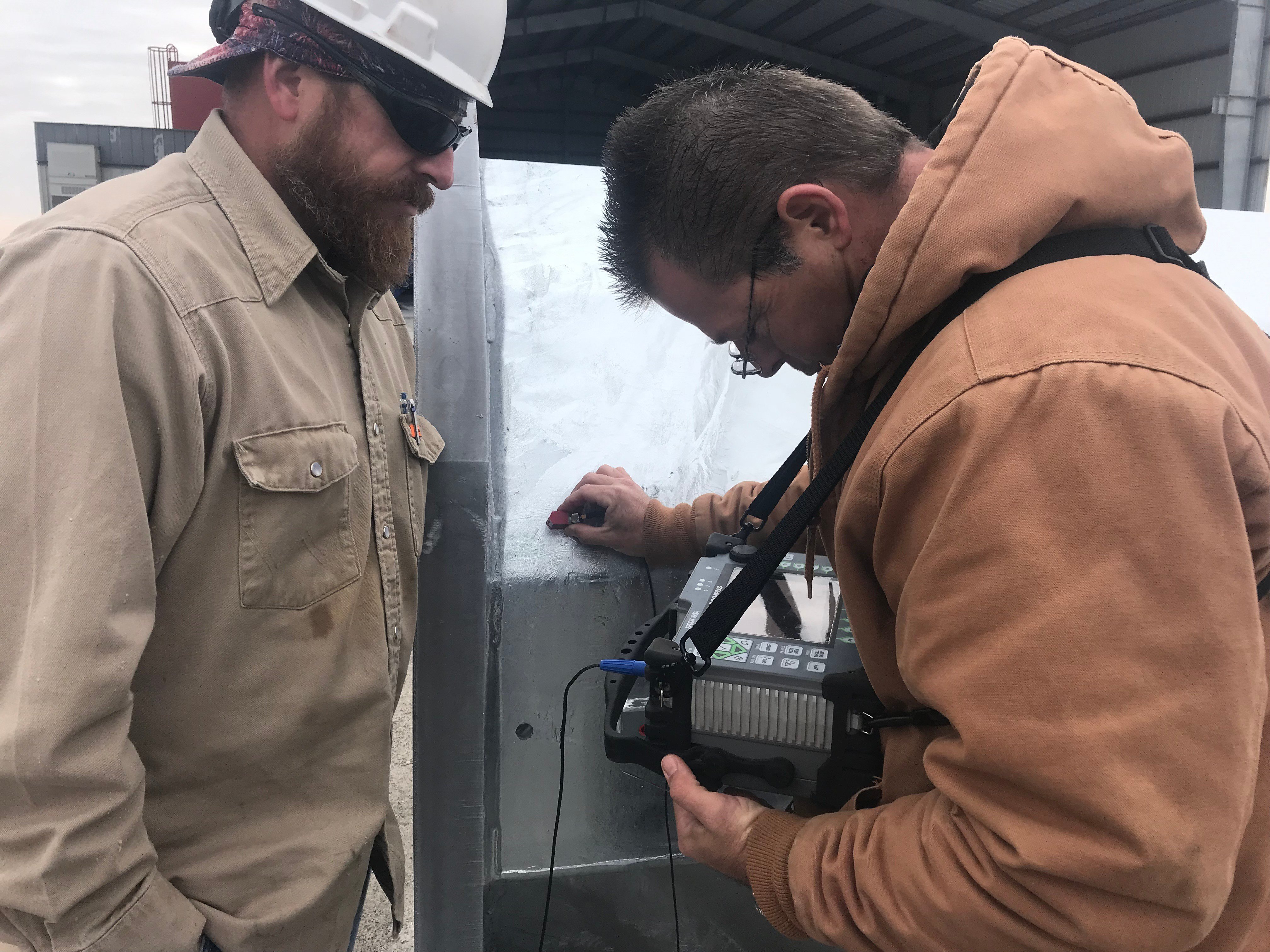
Why is UT Testing Beneficial?
UT testing allows manufacturers to thoroughly examine critical welds, ensuring structural soundness and longevity. UT Testing can reveal specific types of flaws, such as:
- Linear cracks within the material
- Gas pockets or voids trapped inside the weld
- Foreign materials that may have been inadvertently introduced into the weld
- Incomplete fusion where the weld metal hasn’t fully bonded with the base material
Because ultrasonic testing is non-destructive, it allows for the detection of these flaws without causing any damage to the weld or surrounding materials. This provides manufacturers with peace of mind, knowing they can catch even the smallest abnormality before the product reaches the customer. For a look at the different types of welds, check out Mastering the Art of Welding: A Guide to the World of Welding.
Common Challenges of Ultrasonic Testing
While ultrasonic testing is highly effective, it does come with a few challenges:
- Operator Skill and Interpretation
The accuracy of UT relies heavily on the skill and experience of the technician. Reading ultrasonic signals requires interpretation, which may vary depending on the technician's experience.
- Surface Preparation
For ultrasonic testing to work effectively, surfaces must be clean and smooth. Uneven or contaminated surfaces can interfere with sound wave transmission, resulting in inaccurate readings.
- Material Properties
Ultrasonic waves behave differently in various materials, which can make it challenging to obtain consistent results across dissimilar metals or alloyed materials.
How Manufacturers Overcome These Challenges
To maximize UT testing’s effectiveness, manufacturers implement the following practices:
- Advanced Training
Ensuring that technicians receive comprehensive training in interpreting ultrasonic readings is crucial. Many companies invest in specialized certification programs to maintain high standards.
- Regular Calibration of Equipment
Routine calibration of UT equipment ensures accurate readings and minimizes error. Manufacturers often establish schedules to recalibrate based on usage frequency and material variability.
- Use of Advanced UT Technologies
Techniques like phased array UT and automated scanning are used to produce higher-quality images, reduce operator dependence, and enhance defect identification.
Ensure Quality and Structural Integrity
Ultrasonic weld testing is a powerful tool for ensuring the safety and reliability of welded structures across various industries. Its ability to detect hidden flaws without harming the material makes it invaluable for manufacturers who prioritize quality and structural integrity. Understanding how UT testing works and the benefits it offers helps to highlight its role in maintaining the durability of essential components and structures.
Ready to ensure the highest quality and structural integrity for your steel structures? Contact DIS-TRAN Steel today to learn more about our capabilities and how we can help you achieve unparalleled reliability and safety in your projects. Have questions, submit them here.