Today’s companies freely state Lean principles are practiced within their organizations and relay that the application has proven to have significant impact and provided improved results. However, if you really take an honest look there are only very few companies that would be considered “Lean”: Toyota, Honda and Danaher. In my opinion, most companies only seem to utilize a few Lean principles to fire fight, and only as a last resort. Even then, these efforts tend to fade away over time. Lean is much more than just using the principles and tools like 5S, Pull Kanban, Cell Flow, TPM, etc.
So what is missing in the Lean efforts at most companies?
Lean is not simply doing the same things, the same way, with fewer people. Lean is a systematic approach to attain Sustainable Results by identifying and eliminating waste by flowing the product at the pull of the customer in pursuit of perfection. What is missing at most companies is the ability to understand and accept what must happen to achieve a Lean Enterprise Transformation focused on Sustainable Results. In my opinion, Sustainable Results is a function of three interrelated and interdependent parts working together:
- Tools and Processes
- Accountability
- Culture
Sustainable Results = T x C x A
Tools and Processes refer to the body of technical methods used to accomplish the desired metrics. Accountability refers to decisions that define expectations, grant power, verify performance, and consist of specific management and leadership processes. Culture refers to the sum of daily habits. Sustainable Results can best be represented by the Lean Business Model below.
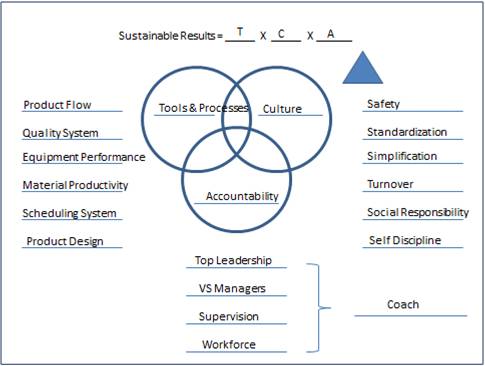
Guest Blogger: Roger Caldwell, Program Manager – Manufacturing Assistance Program at Texas A&M Engineering
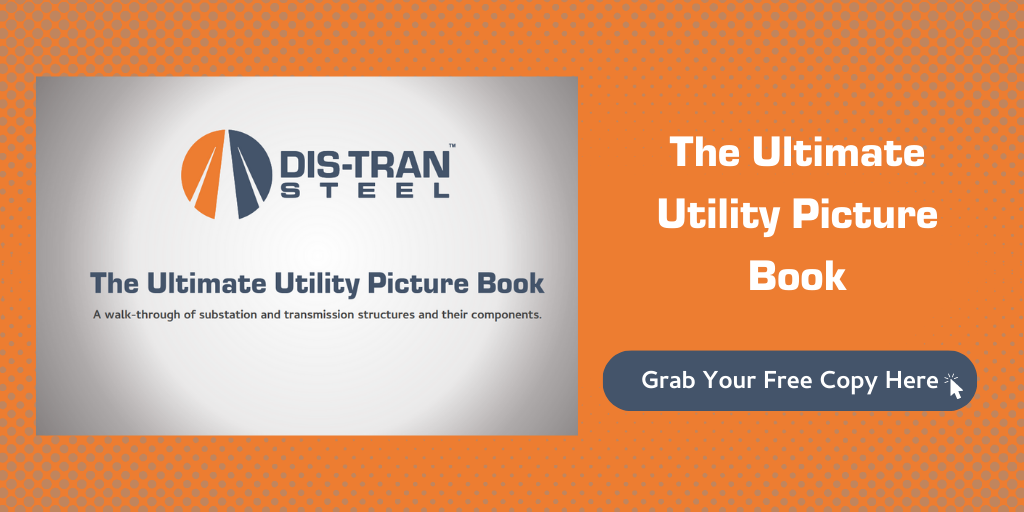