Growing up as a kid, I’m sure you heard one too many times, “Get down from there! You’re going to hurt yourself!” Or as an adult, how many times have you caught yourself saying the exact same thing? Safety is subject we all understand, but it’s also a concept that we think we’re invincible to.
No matter if you’re driving down the road, playing football in the backyard, hunting or even just riding a bike-safety precautions are there. When you’re welding, seaming or picking up and moving 1,000 pound steel structures, you wouldn’t believe all the possibilities that could potentially happen if safety isn’t implied. An accident, as stated in the dictionary, is an unfortunate incident that happens unexpectedly and unintentionally, typically resulting in damage or injury. Well, without safety procedures, precautions and rules, the word accident would become an understatement.
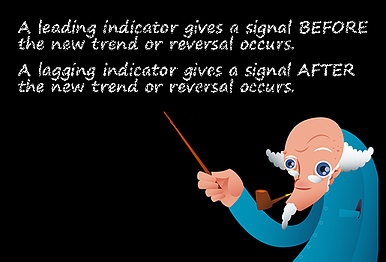
The Leading versus Lagging Indicator approach is a proven technique that can easily be implemented no matter what industry you’re in. Lagging indicators measure past performance, failures and other safety factors, while leading indicators measure current events that keep accidents from occurring.
Looking at past performance is reactionary, where as looking for leading indicators to prevent accidents before they happen is being proactive. There are many ways to measure leading indicators, which can vary depending on the type of products being manufactured, in-house machinery being used, number of employees and so on.
Below are 5 examples of leading indicators that can be measured and tracked.
1. Audit Scores- A walk-through is conducted in order to identify any hazards that are currently happening, such as employees not wearing their proper Personal Protective Equipment (PPE), lifting or handling material incorrectly or trash on the floor. An audit is a great way to spot problems that can lead to accidents because a weighted score is given, which can then be used to pinpoint issues and track progress.
2. Behavioral Observation Cards- This method allows for employees to recognize issues themselves, and then document what it was. It helps train their minds to be more conscious of not only what’s going on around them, but how they too can improve their safety. If you’re company has monthly, quarterly or yearly safety incentive programs, then this leading indicator can be tied to it.
3. STOP Cards- Taking the observation cards a step further, STOP Cards require the employees to make actual safety stops and document them to turn in. While this is to remain anonymous so employees don’t feel betrayed by their fellow employees, the use of positive reinforcement in leading indicators may produce a more forthcoming workforce and culture. This also provides leading information to help derive where safety efforts and dollars need to go towards.
4. Employee Perception Survey- This survey provides feedback to the employer on how the employee feels about their personal safety while on the job. It’s important for the employees to feel safe while they are at work, and if they don’t, then something needs to either be changed or corrected. It is the responsibility of the employer to ensure a safe work environment, which in return, turnover rates decrease, employees are happier and work performance increases.
5. Training Programs- It’s a known fact that trained employees are safer employees. That is why OSHA requires mandatory training on certain things such as driving a forklift. But it can also be beneficial to implement your own training, like a “Tool Box Talk” that requires your employees to learn specifics about the machines and materials they are handling at your facility. Another idea is to OSHA certify all employees and require them to attend weekly training meetings, and after training is complete, performance can be tracked (leading indicator). The more training, the better and safer your employees will be at their jobs.
In order to create a positive working environment for all employees, it is important to assess and enhance safety conditions. Employees must feel both physically and emotionally safe from harm, and that their employer truly cares about their safety. But they must also be equipped with the safety skills to handle situations that may arise. It’s important that all employees feel engaged and challenged in their working environment, with high expectations set for all.