
Every year the U.S. spends $350 billion replacing corroded steel.
BIG PROBLEM: Corrosion increases taxes $2.2 trillion annually, which is 3% of the GDP (gross domestic production). And what’s even more frightening is the $1.6 trillion needed investment in order to bring up the nation’s infrastructure, which translates to 27% of the bridges in the U.S. To dig deeper into that number, about 160,000 bridges across the country are in need of repairs. Over the decades, many have done the “patch and pray” method, instead of properly maintaining steel structures.
Clearly you can see that corrosion is a major problem. So what is the solution?
Galvanizing is the process of applying a protective zinc coating to steel in order to prevent rusting and corrosion. The zinc acts as a protective coating by forming a physical barrier and by acting as a sacrificial anode even when the barrier is damaged.
The most common method used today is hot-dip galvanizing, in which steel parts are submerged into a bath of molten zinc. Galvanizing creates a coating that is actually stronger than steel and has an extremely long maintenance-free service life.
Benefits of galvanizing:
- Barrier protection resists corrosion by isolating the steel from electrolytes in the environment
- Alloy and zinc iron alloy layers are stronger than steel, providing superior durability
- Extremely economical-less expensive when compared to the maintenance costs that would have been needed
- Corners and edges protected because coatings grow perpendicular to the surface
- Coating applied inside and out (ex: tapered tubular poles)
- Environmentally friendly compound-zinc is a natural element in the earth’s crust
- Sustainable-zinc and steel are 100% recyclable
- Availability-24/7/365 without temperature or humidity requirements
- Variety of shapes and sizes
- Process is inclusive of all cleaning, materials and labor
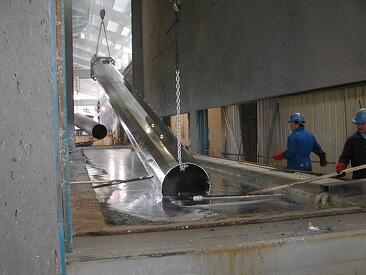
If you look around, we encounter galvanized steel on an everyday basis. The Texas Motor Speedway, the Botanical Gardens or the Baltimore Ravens Stadium, and even down to irrigation systems and street signs; all of these steel structures are galvanized.
One big misconception about galvanizing is that it is a “paint job.” It’s assumed that if one portion of the steel comes out bright and shiny and the other is dull and grey, then the duller area must be defected or not up to code. But the truth is that it just depends on the steel composition, and there is a good chance the duller portion contains more zinc. The discoloration has nothing to do with the sustainability of the steel, it is strictly aesthetics.
There are 4 different types of coating appearances:
1.) Shiny
2.) Matte grey
3.) Spangled
4.) Shiny and dull
Galvanizing has been a proven method and has been around since the 17th century, and was patented by Stanislas Sorel of Paris, France in 1837. The process of galvanizing is very thorough and unique, and has an unmatched reputation. To learn more about the 4-step process of galvanizing, click the link below.
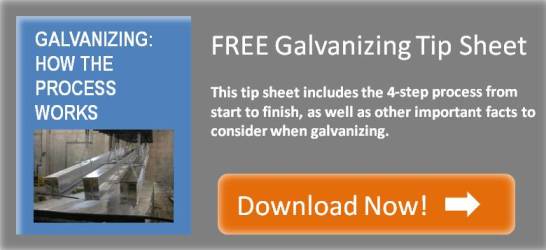