Every manufacturer wants their product to be at the world-class level, but the question is “Can you compete at that level?”
Lean Manufacturing has been around for some time now, and has become an essential tool, especially for production facilities. Introducing Lean Manufacturing can significantly reduce waste and enhance quality and delivery.
So how can you bring the best value to your customers?
From our experience, the 6S System has been the foundation for all other Lean activities. Once the problems have been identified and a solution has been formulated, then the next step is to create Standard Operating Procedures (SOP) in order to sustain an organized and functional area.
*An operation must develop an organized work place with standard operating procedures in order to feed its continuous improvement culture.
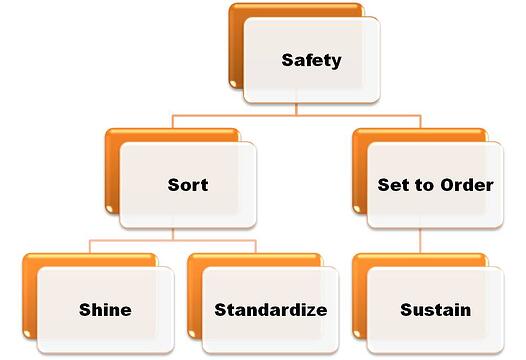
The 6S System:
1.) Safety - Develop and implement JSAs for all of the processes involved in operation
2.) Sort - Keep what is needed and systematically remove what is not
3.) Set to order – a place for everything and everything kept in its place when not in use
4.) Shine - clean the equipment or area to keep in “new” condition, and inspect the equipment for repairs during the process
5.) Standardize- Develop processes that maintain the first 4 S
6.) Sustain – Develop processes that motivates employees to maintain the procedures. Also involves creating audits, SOPs and other tools to check for progress and maintenance of the standards.
Implementing the 6S system can be difficult because many companies are set in their ways, but if you keep up with the process, over time the culture will progressively evolve.
Follow these seven steps to discover the problem areas and solutions.
First, identify the areas that need attention and improvement and then outline the concerns and the solutions.
Second, form a diverse core team. You’ll want someone who is familiar with the machines, someone from outside who can look on with fresh eyes and someone who can facilitate and make decisions.
Third, choose a strategic location. If this is the first time, choose a location with obvious problems that you know you can have success with.
Fourth, identify the problem and describe it in a problem statement.
Fifth, conduct an audit or scan of the selected area.
Sixth, photograph or video major problem areas.
Seventh, assign action to team members.
Once the area is organized and running efficiently, this is where developing an SOP comes into play, as well as work instructions. Work instructions are typically one page and are a supplement document to SOPs. They explain several steps such as how to start up the machine, operate it properly and what to do if there are problems.
The benefit of developing an SOP is that, regardless who the operator is, the product is still being produced the same way each time. This not only finds the areas that are insufficient, but adds value and quality to the final product.
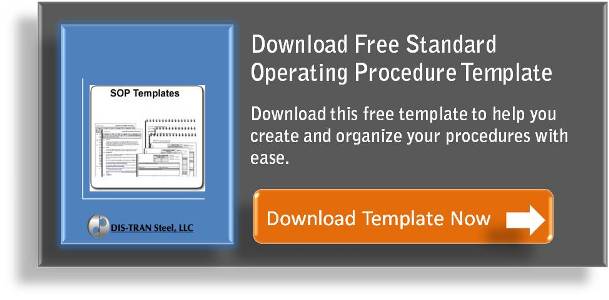