Around now for over 10 years, Lean Manufacturing has proven to be an essential tool. The concept is black and white: eliminate waste to improve the overall value.
Makes sense, right? So, how does one go about doing this? The answer: Value Stream Mapping.
A Value Stream Map identifies waste within and between processes, and then determines a plan for finding the bottleneck areas to eliminate them. It also can help to control inputs and monitor outputs.
So what is Value Stream Mapping?
Instead of just “guestimating” what areas are not working, a Value Stream Map lets you see the process from a bird’s eye view. It visually shows each step in each process and then how it is communicated. It allows you to prioritize which key areas or initiatives need to be addressed first, and also lets you set goals to reach. Once you do this, you find where waste is created.
Value Stream Mapping looks at the material and information flow within that value stream. It also looks at the steps within the scope of the operations. Once that initial stream is created, data is then gathered for each process step. Data such as:
- Value Added Time
- Downtime
- Right the First Time
- Cycle Time, etc.
This data is then evaluated for waste reduction/elimination opportunities. Once those opportunities are recognized and prioritized, the process of developing a Future State Map needs to be created.
The future state should be a working document, something that is easily reviewed, improved and used on a regular basis (perhaps weekly). During this review process, the Future State is always changing-creating more opportunities. This is not a document that you file away.
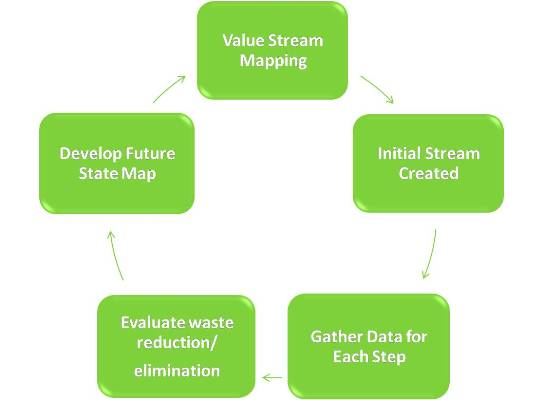
How to Implement a Value Stream Map:
- Identify the product
- Construct a value stream map of what’s happening currently on the shop floor- procedures, delays, production flow, etc.
- Assess the current state value stream map
- Draw a future state map
- Work towards future map
Understanding Value Stream Map:
- Create a list of products
- Group them into families
- Determine each product to be considered primary
- Document the steps of the process
Lean isn’t just a hunt to find where waste is occurring, but it’s also used to prevent waste before it ever arises by implementing the principles and adding value to your process.
5 Main Principles of Lean Manufacturing:
1.) Define values perceived by the customer
2.) Identify the value stream
3.) Make the Value Stream Flow
4.) Flow at the pull of the customer
5.) Strive for perfection