Just like fuel is needed for an engine or a bowl is needed for soup, communication between the steel supplier and receiver throughout all processes is essential.
Getting from point A to point B seems like an easy task, but when it is assumed rather than confirmed, you could run in to some problems. Shipping steel structures is an important piece of the puzzle.
The first, and what some would argue the most critical part when shipping, is to contact the customer to first let them know that their order is ready, as well as confirm the location that it will be shipped to. Next, the Bill of Lading should be checked to ensure that there are the correct number of pieces, pieces marked and weight.
Following that, it should be determined, or estimated, how many truckloads it will take to load and deliver all the material. The next step is to contact a carrier who either offers the best rate and service. The supplier should make sure that whichever carrier they choose, they should be experienced and know route planning, permitting and the delivery process.
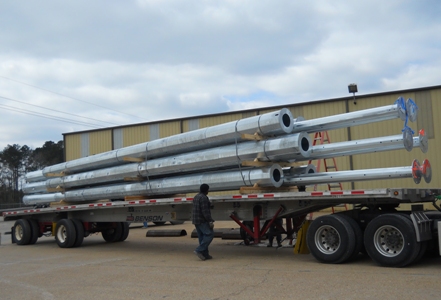
Ok, I know that sounds simple, but there are several deadly sins to stay away from when shipping steel structures.
- Never ship assembly bolts on any other truckload than the first one. Why? Well, without the bolts, the customer cannot begin to assemble any of the structures.
- Don’t ship anything out that has missing pieces on the Bill of Lading, because this could hold up the project.
- Don’t ship without checking the structures’ cosmetic outer coat for obvious blemishes or defects, as this could hold up the project even longer if the customer doesn’t approve or if it needs repairing.
- Loads should not be cubed out. In other words, the structures must all be within the 8 x 8 “cube,” and if any poles or structures are over length, then the carrier needs to obtain an oversize load permit.
- Truckdrivers should never deliver to the jobsite before they pre-call the customer contact to confirm delivery time. (The customer contact and phone number is always typed on the Bill Of Lading.)
- Never ship anything overweight. Maximum weight is 40,000 to 45,000 LBS per truckload.
- Above all, the load must be loaded safely. It is up to the driver to determine whether or not the load is loaded correctly and can be hauled safely.
If the receiver requests for the structures to be delivered in a specific order, it is important to communicate this between the project coordinators, shop and shipping department to ensure this happens. If not, it could end up costing the receiver lost hours as well as delays in the project. For example, they shouldn’t receive insulators and switches before columns and switch rack mounts.
Safety is another concern when loading a truck. It’s critical to make sure the straps are secure, and that all material is locked in place. Also keep in mind that when dealing with tubular steel structures they can sometimes shift during delivery, which could create the danger of rolling.
All of the steps listed above can help a delivery run smooth and efficient so that the supplier, as well as the receiver, both experience a stress-free operation. Also, remember it is important when choosing a carrier, because once that truckload has left the premise, it is their responsibility to get the materials to the receiver in a timely and safe manner.
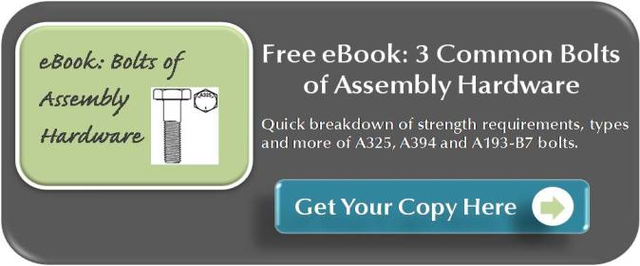