DIS-TRAN Steel takes pride in being able to offer two types of products. We manufacture both tapered tubular structures, “pole”, and standard shape structures, “fab”. We treat the two as their own “product family” within DIS-TRAN Steel and it can sometimes cause confusion for customers when they have a project involving both. We want to try to clear up some of that confusion and provide what we do best: transparency.
The pole product family serves both the transmission and substation industries.
On the transmission side, there are three main types of pole structures:
-
-
- Tangent – These are the majority of transmission structures that are seen and are used when the transmission line is going straight.
- Angle – This type of structure is used when the line is going at a slight angle.
- Dead end – These are used when the line is at an extreme angle, terminates, or crosses over a major road crossing.
There are also three main types of pole structures found in substations:
-
-
- Static mast – A single pole that protects the substation from lightning
- Substation dead ends – These can be A-frames or H-frames and receive the incoming transmission lines into the substation.
- Higher V equipment stands – Stands that support various substation equipment such as switches, CCVTs, etc.
The fab product family mainly serves the substation industry and will typically be utilized for low-profile equipment structures. These are the structures that go inside substations to support common equipment like insulators, CVT stands, and any kind of instrument transformer.
*Learn more about the different types of structures and supports in our eBook “Beginner’s Guide to Substation and Transmission Steel Structures”.
Why Separate?
So why do we separate pole and fab structures when they’re both products of DIS-TRAN Steel? The two are primarily run as two separate businesses so we can deploy all the resources needed to each product family to deliver a quality product with top-level customer service and transparency throughout the entire process, while helping the customer meet their project budget. The decision to split the two into separate departments stems from the fact that they have entirely different manufacturing processes. At our production facilities, the two have their own shop buildings to keep things on track with manufacturing of the two different products. Dividing the processes allows each group to run as efficiently as possible. Each shop can maintain its production capabilities regardless of any changes in the other product’s manufacturing. It also allows us the ability to pay more attention to each individual product and make continuous improvements that directly affect that product line.
Another difference between the two is lead time. Overall, lead time for poles tends to be longer due to a few key factors:
- Design Process: Pole structures have a lengthier lead time overall due to the fact that they require more upfront work. Many customers have libraries of fab structures they have been using for years and just need to be built. Pole structures, however, require additional steps before being ready for manufacturing. They are usually application-specific, requiring analysis of the loads needed for the conditions of the project. Engineering resources are responsible for the calculation and designing of the structure, followed by a detailing group that creates the fabrication prints. Then it is ready to be sent to the shop.
- Custom Manufacturing: Pole structures are typically manufactured from flat sheets of steel that must be formed to meet the customer’s needs. This adds additional steps, such as cutting the profile, using a press break to shape the material, and assembling the pieces. This custom manufacturing process prolongs lead times. Fab structures on the other hand are made from common industry materials such as wide flange, tubes, and angular shapes that are usually readily available. This eliminates the need to form the materials from flat sheets of steel and speeds up the manufacturing process.
- Market Influence: An increased demand for poles, particularly in transmission and substation applications, can result in extended lead times, even if all the upfront work is complete. Sometimes we receive orders that are already designed and just need to be manufactured, however, this may not help speed up the overall process. The backlog of orders currently at the shop can lead to delays, causing extended waiting periods even if the structure came in pre-engineered.
The separation of the Pole and Fab product families provides the ability to allocate more resources for delivering specialized manufacturing processes and maintaining top-level customer service. Want more information? Contact us today with any questions you have and to learn more about our current lead times.
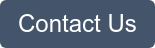