“How do I successfully touch-up galvanizing in the field?” This is a common question about substation and transmission structures. There could be a number of reasons why touch-ups may be necessary in the field.
- Extremely rough handling
- Installation techniques
- In-service conditions
There are certain factors to consider when repairing galvanizing in the field, such as: the size of the area to be repaired, the ease of use of the repair material and the performance of the repair method. There are also standard specifications to follow for the repair of galvanized coatings. ASTM A780 covers methods used to repair damaged hot-dip galvanized coating on hardware and structural shapes as well as required coating thicknesses. There are three acceptable forms of touch-up.
- Zinc Based Solders- achieved by applying zinc alloy by stick or powder form. Most common alloys are zinc-tin-lead, zinc-cadmium and zinc-tin-copper. To prepare the surface use a wire brush, lightly ground, or mildly blast clean and remove all weld flux and spatter. The area being repaired needs to be preheated to 600 F. This is the most difficult method of repair.
- Zinc Rich Paints - either by brush or spray is applied to a clean, dry surface. The paint must contain between 65% to 69% metallic zinc by weight or greater that 92% by weight in dry film. To prepare the surface the area must be cleaned either be blasted, power tool cleaned or even hand tools (wire brush). This is the most commonly used field repair method and can easily be done without a need for blasting or power tools. Zinc-rich painting should be avoided in high humidity and/or low temperatures.
- Metallizing - achieved by melting zinc power or zinc wire in a flame or electric arc. The zinc used is minimum of 99.5% pure. To prepare the surface it must be blasted cleaned to SSPC-SP10/NACE No.1 near white metal and must be free of oil, grease, weld flux residue, weld splatter and corrosion products. The cleaning must include surrounding, undamaged coating. Spraying should be done by a skilled worker in horizontal overlapping lines to create a uniform thickness. Not recommended for high humidity locations.
The coating thickness of the repaired area must match the coating thickness of the surrounding area. If zinc-rich paint is used, the coating thickness must be 50% higher, but not greater than 4.0 mils.
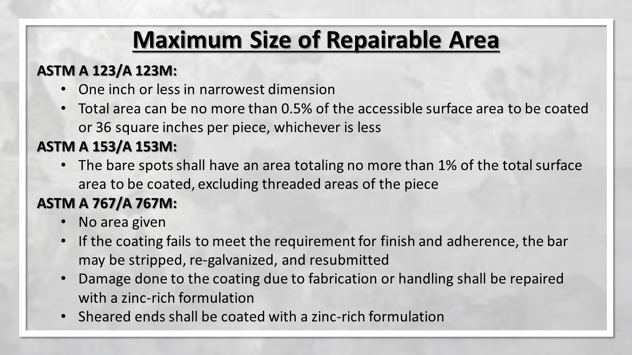
Be sure to discuss any touch-ups with your steel fabricator or galvanizer. They may have suggestions on which method has worked best for certain circumstances. Final coating thicknesses need to be agreed upon between customer and vendor and be measured by the methods in ASTM A 123/A 123M. Remember that the surface of the repaired coating should be free of any lumps, course areas and loose particles.
For more about galvanizing check our our free and easy resource - Galvanizing Ebook below.
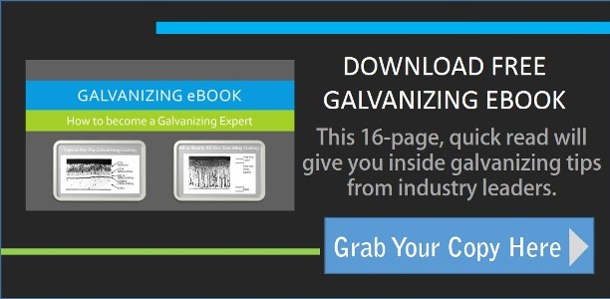
*References used for this article are from www.galvanizeit.org.