We all appreciate on-time delivery. Whether it’s ensuring your new G. Loomis fishing rod is in before your next tournament or Amazon delivering your new sandals before you head to Florida; we all depend on the supplier.
It’s critical that the supplier is organized, flexible and has an updated production backlog to make sure delivery is as promised, and not late because they have over-committed themselves.
A backlog is the total production that remains to be completed at any given time. It may also include some tentative work that you are fairly sure you will be awarded, although you may not have an official purchase order yet. The sold production is prioritized into a production schedule over the coming months depending on size and the promised delivery date.
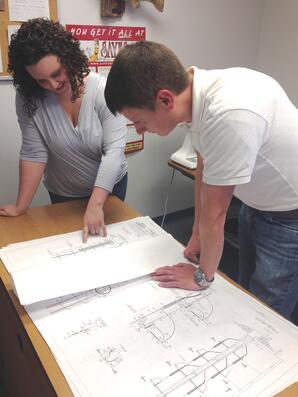
The backlog is important to all of the departments within an organization, all the way from estimating, to engineering/detailing, production, etc., so that each promised job has its required amount of resources available and scheduled before the fabricator promises any additional deliveries. It must be updated constantly as new jobs are won. Any company who prides itself on customer service and on-time delivery must have a defined backlog that is current and that has been set to achieve 100 percent of promised commitments.
The backlog allows the estimating department to know exactly how much and where any capacity is available in any given month so that they can make their next commitment to a customer on the next project they are bidding on. It will show any “holes” in the schedule where something may be worked in. It will also show “premium hours,” such as weekends, that may be available for customers who have a project that requires an expedited schedule where overtime fees are acceptable to meet the required delivery date.
But as easy as filling a backlog might seem from the outside, it can get a little difficult and sometimes frustrating to the customer and fabricator.
Problem #1: If a customer knows that there is a specific size project coming up for them in the future and roughly when they will need it by, but say the market is so busy, that their chances of getting their project by the desired time is slim once the details are finalized.
Solution: Fabricators can hold production space for customers based on a rough idea of the project scope and often without an exact purchase order for particular projects. If the customer knows when they need it delivered by and can estimate the scope of the project, then the fabricator will bid other projects around it as if the project remains on track. This is beneficial to both the supplier and the customer. However, if the project schedule changes, this results in challenges for the supplier due to backlog holes.
Problem #2: Backlog holes can sometimes be one of the more frustrating aspects of managing a production backlog. Holes in production can come from many sources, such as slow bookings, project slipping or approval hold-ups. A backlog hole is a period when there is not sufficient work scheduled to meet the facilities capabilities. This results in lost revenue for the facility and lost productivity.
Solution: From a customer’s prospective, this can be beneficial because if their project “needs” fit the supplier’s “wants” they could get their project at a really good price, a really good schedule or both! Make sure to always stay in contact with the supplier’s estimating department because opportunities like this might arise that work for both.
Problem #3: Often during the normal course of a project, various issues can cause the project schedule to slip. When this happens the project now moves out into the next future open spot in the schedule. If the backlog schedule behind the slipped project is full, the next available production spot could be several weeks out. Often, as a customer, it can be hard to understand how only a week delay in the project schedule can result in a month or longer delay in production. But it’s similar to getting out of line for an amusement park ride and then coming back to find the line has taken your spot and now you have to get behind everyone else. The issue for the fabricator is that the schedule slip could result in an open backlog hole that is unable to be filled, resulting in productivity loss.
Solution: These cases don’t necessarily happen all the time, but when they do, they can be frustrating for both parties. Frequent open communication between the customer and supplier often goes a long way in alleviating this issue. Strong relationships between the customer and supplier or having an Alliance Partnership definitely doesn’t hurt in times like these, but other solutions like expediting can be arranged. The fabricator can bring in extra crews, work overtime, expedite shipping-anything to help ease the pain of this problem. (Expediting fees might be included though.)
Problem #4: Typical suspects for project scope change are engineering changes or customer revisions, which result in either an increase or decrease in project scope. When changes become significant, the backlog schedule is impacted either by the production slot being overfilled (for increases in scope) or under filled (for decreases in scope). The overfilled production slots often result in split deliveries, with some material delivered on the original schedule and the balance delivered at a later time based on the remaining backlog. If the scope of the project is reduced and the supplier is unable to fill the resulting backlog hole, there will be a financial impact to the bottom line.
Solution: By doing strong research, or “homework” on the front end, and not changing the project after it’s been ordered can help alleviate this problem. Staying in constant communication with the fabricator during the quote stage can also help iron out issues before they happen.
Problem #5: Another backlog gremlin is when Murphy ’s Law attacks the project with unforeseen fabrication issues. Most experienced fabricators are able to negate normal production issues with production buffers and preventive maintenance programs. However, there are times when either a new product type slows typical productivity, or overly difficult fabrication results in an underestimation of required production backlog time. Despite the supplier’s best intentions, these issues do occur at times.
Solution: Make sure that the fabricator has adequate capacity and experiencein the industry. Plant tours, sales visits or even just phone calls and emails exchanged can help build relationships and trust. Developing a relationship with a fabricator who will be open about any fabrication issues can go a long way to ease any construction scheduling delays as well.
The good news is that often most of these backlog issues can be remedied by upfront and direct communication between the customer and the supplier. With adequate notice, suppliers are usually able to adjust backlogs to suit project delays or scope changes.
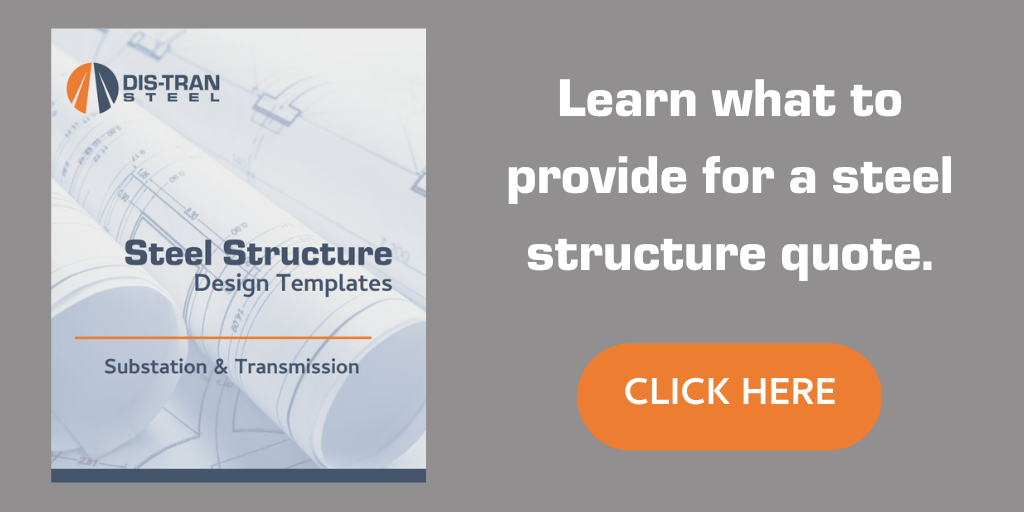
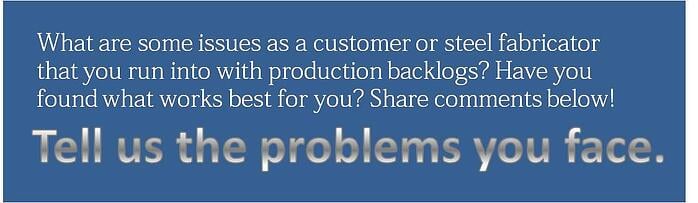