Culture is a powerful thing. It affects the way we think, operate, our instincts and reactions.
The culture inside a manufacturing facility tends to be a little more “macho,” rather than say the culture inside a daycare center. But in both of these scenarios, safety is the number one priority.
It’s not human nature to put something over our hands, especially when we are using them to work. Culture might have taught us this slows the production process down or creates a distraction. But hand injuries could have serious effects down the road.
Let’s say someone on the production line gets a cut or abrasion from not wearing proper protection while working. This could further lead to stitches, infections, soreness or other medical treatments. So now, they might be on light duty, can’t work as fast or even out of work for a while. This could have an indirect and direct cost.
Indirect cost- Work slower, have to hire someone else in the meantime
Direct cost- Doctor bill, Worker’s Compensation
Although hand safety seems like a minor issue when you’re looking at the entire scope of safety in manufacturing, hand injuries can easily be prevented if the proper steps are taken.
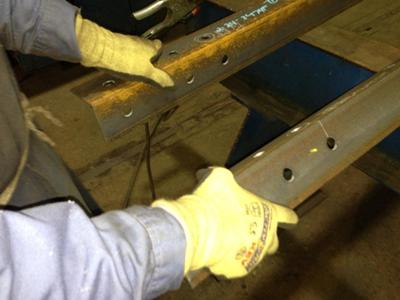
Listed are five steps to help ensure that the proper protection is provided.
Step 1: Organize a Continuous Improvement Process (CIP) and look back at the hand injuries that occurred over the past five years and conduct a route-cause analysis of each injury to determine how it could have been prevented if proper gloves were worn.
Step 2: Have an external consultant come in and conduct a Hand Safety Analysis to analyze the different operations, job functions and practices, and then recommend what types of gloves and/or hand protection are needed.
Step 3: Order different samples of gloves based off of the Hand Safety Analysis.
Step 4: For one month, track each pair of gloves. Make sure to track what area of operations they’re being used in, the employee wearing them, how long they lasted and if there were any malfunctions.
Step 5: After each sample has been evaluated, determine which glove works best for your particular process or operation.
By providing the proper protection to your employees and requiring them to wear it, not only ensures their safety, but it boosts the moral of the entire facility- thus helping change the culture. Analyzing the process and taking the proper steps proves for a more efficient and productive atmosphere.