Something that might be viewed as a small, insignificant venting hole on a 10,000 pound structure, if not well thought out, could really have an adverse effect on production.
We all make mistakes every now and then; no matter if you’re on the engineer side, or project coordinator, quality control or detailing side, mistakes happen. But these mistakes, big or small, can delay or put a halt to jobs. I know it’s easy to sometimes overlook something when we’ve done it so many times to where we could practically do it in our sleep. But nonetheless, you have to make sure to keep an eye out and to catch mistakes before it gets too far down the production line.
When creating fabrication drawings for galvanized structures, it’s important, as well as valuable, to know proper draining and venting provisions for these steel structures. If adequate venting and draining holes are not provided, these structures can run into many problems.
5 Negative Effects:
1. Air pockets can form, causing structures to rust out from the inside
2. Excess galvanizing buildup
3. Lead to longer fabrication times
4. Welded plate can blow out, causing safety concerns
5. Poor coating
It’s key that along the process, there are people in place who know what to look for or have an eye for knowing what will work when it goes to the galvanizer. But if it passes through the line of engineering, detailing, quality control and then is delivered to the galvanizer, it might be harder and more costly to make modifications. Plates might already be cut or everything might already be welded up, making it more difficult to modify.
Not having adequate venting and draining holes can really have an intangible effect. It’s hard to put a dollar amount on what happens when a structure either doesn’t have proper venting, or one of the five stated above occurs. It’s usually not too hard to correct if it’s caught up front, but the further it gets in the process and closer to delivery dates, is when you might start scrambling. All the man hours it takes to call the engineer on record to approve revisions, or contact customers, plant personnel, the galvanizer, etc. can really put a stop to production, causing low production numbers and possibly delayed shipping. But working with a trusted steel fabricator, can help to avoid these issues.
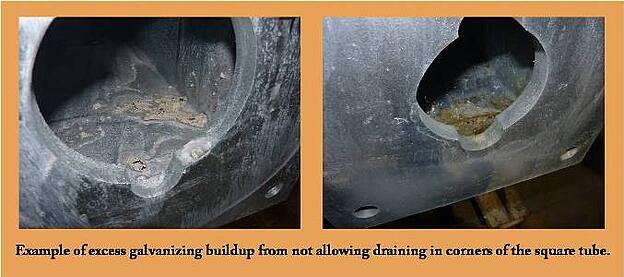
Some standard shape structures, such as square and rectangular tube columns and beams, are hollow, so provisions need to be made in order to allow galvanizing to easily flow and coat the inside portion of the structure. Other standard shape structures, like channels, wide flanges and angles, are solid so just the outside receives coating, which means air pockets and excessive galvanizing buildup can form. For these shapes, you need to watch where stiffeners, connection plates and brackets are welded that could form large pockets of air as the section is dipped into the kettle. Tapered tubular structures are the same as square and rectangle tubes, in the sense of being hollow.
For standard shape and tapered tubular structures, using removable cover plates on the ends of beams is a good option instead of welding solid plates to the ends. This allows for faster flow through the member and more adequate galvanizing.
Now, also to keep in mind, ensuring proper venting doesn’t mean place a bunch of holes all over the structure, but rather strategically supply the venting and drainage provisions. For example, if dealing with corners in a square and rectangular tube, slots or holes can be provided near these corners to prevent air pockets from forming, which can decrease the amount of galvanizing coating in the area.
The more you understand how the member is lifted and dipped in and out of the galvanizing kettle, the better you can locate the venting and draining provisions. As a designer, you are always trying to find the balance of putting enough holes for galvanizing while not putting too many to affect the structural integrity of the steel member.