In last week’s post I outlined the 5 different grades of zinc used for hot-dip galvanizing; LME, SHG, HG, IG, PWG. So, following that, what changes the appearance of the galvanized steel?
Most steel materials can be hot-dip galvanized such as cast iron, malleable iron, cast steels or hot and cold rolled steels. Structural steel shapes can also be galvanized after fabrication to provide a protective coating.
When the steel enters the kettle at 840 to 850 degrees Fahrenheit, zinc-iron alloy layers start to form. This portion normally represents about 50 to 70 percent of the total coating thickness, with the zinc being the top layer. Directly coming out of the kettle, all steel is extremely bright, despite the coating appearance.
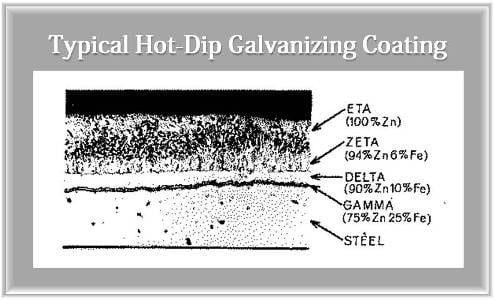
And if you remember, no matter which grade of zinc that’s used, all galvanized steel will start to dull after about 6 to 8 months. But if the steel is spangled, it will still have that appearance over the service life, just not as bright.
The characteristics of the galvanized coating is affected by the chemical composition of the steel material that is being used. The coating appearance can come out shiny, matte gray, spangled or shiny and dull. These are simply cosmetic issues despite the color variation.
The composition of the steel varies depending on the strength and service requirements. Certain elements in the steel can affect the galvanizing technique, as well as the structure and appearance. For example, steel with higher silicon is more reactive and tends to give that spangled look.
When purchasing steel from the mill, there are certain parameters or guidelines you should follow in order to select steel with good galvanizing characteristics. You can also request a Mill Test Report (MTR), to see if the parameters are in the requested range. When it comes to structural steel however, it is not as controlled since you’re buying from a warehouse.
The chemical content of the steel determines the zinc-iron alloy coating. If the coating appearance is bright or splotchy gray, this is due to an excessive amount of certain chemicals that you need to be careful of. However, the splotchy or matte gray appearance is not grounds for rejection, and actually, the gray areas usually have more millage than the bright silver portions because the zinc continues to grow.
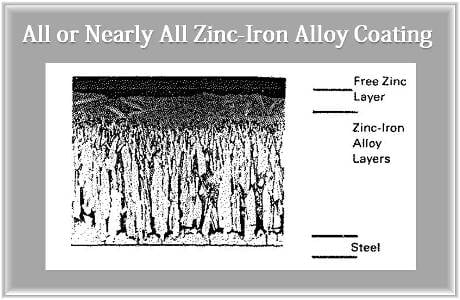
Below is a description of the characteristics of an all or nearly all zinc-iron alloy coating.
Visually The zinc-iron alloy coating will have a matte grey appearance due to not having a free zinc layer, since the free zinc layer typically is what gives the bright finish.
Adherence When compared to the “typical” galvanized coating, an all or nearly all zinc-iron alloy coating may have lower adherence, and tends to be thicker. There might be a reduction of adherence as the thickness increases.
Corrosion Resistance Galvanized coatings are specified more for their corrosion resistance rather than appearance. Fabricators and consumers should be aware that whether a gray or matte appearance occurs, it does not reduce the long term atmospheric corrosion protection of the steel. The corrosion resistance, mil for mil, of these coatings is equal.
Want to know the guidelines that usually result in the selection of steel having good galvanizing characteristics?